Tout savoir sur les caractéristiques du verre plat
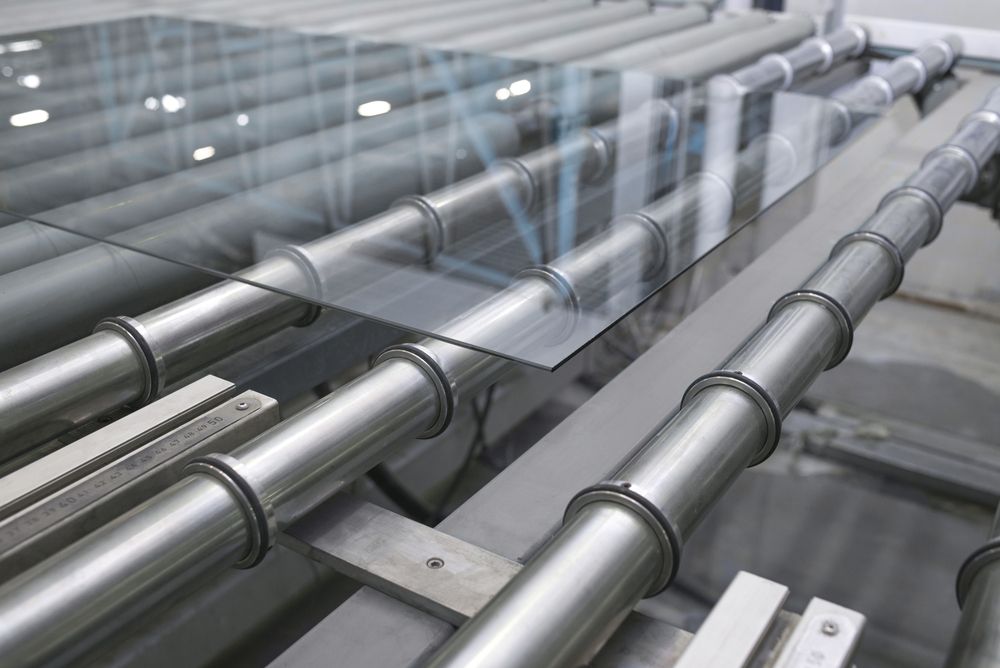
En opposition au verre creux regroupant les emballages, bouteilles, pots et vaisselles, le verre plat affiche une forme plane, fabriquée sous forme de feuilles. Une famille qui s’apparente en grande majorité aux types de verre utilisés dans le bâtiment. Il se distingue des fibres de verre et des verres cellulaires par son processus de fabrication et son rendu transparent idéal pour la conception de fenêtres. On peut y dénombrer toutes les classes de verres de sécurité, qu’ils soient armés, feuilletés ou trempés.
Verre plat : principe de fabrication
Réalisé avec une base de matières premières naturelles telles que le sable et le calcaire, la composition la plus fréquente du verre plat est le verre silico-sodo-calcique. Tout débute au travers de la fabrication de la glace. Autrefois coulé sur table, le verre a été créé à partir de techniques de soufflage dès le XIIe siècle. De nos jours, il est le fruit de deux procédés :
La méthode TWIN :
Les différents éléments entrant dans la composition du verre sont fondus dans un bassin à une température d’environ 1550 °C. Une fois le verre en fusion obtenu, celui-ci s’écoule à l’aide de deux rouleaux lamineurs en un ruban de verre ininterrompu. Il subit ensuite un refroidissement lent et étudié dans une étenderie de manière à le préparer à la phase de découpe. Entre alors en marche le procédé TWIN qui va permettre de traiter la glace brute recueillie afin de l’usiner simultanément sur ses deux faces, d’où son nom de TWIN (jumeau en anglais). Le verre ainsi transformé en glace doucie doit encore subir une opération de polissage pour arborer une parfaite transparence lors du résultat final.
La méthode FLOAT :
Une fois fondu et débarrassé de ses bulles gazeuses, le verre liquide acquis suite au mélange des matières premières entre dans un four contenant de l’étain en fusion pur. Le verre avec sa composition moins dense que l’étain va flotter sur le métal en formant un ruban d’épaisseur variable, d’où le nom de FLOAT (flotter en anglais). Le polissage du verre s’effectue de manière automatique par l’action du feu sur sa face supérieure et par le contact avec l’étain en fusion sur la face inférieure.
Une fois suffisamment rigide à la sortie du four avec une température avoisinant les 620°C, il est ensuite inséré dans un tunnel de recuisson appelé étenderie pour le préparer à la découpe. Une fois refroidi lentement à l’air libre, il est redimensionné en plateaux et prêt pour le stockage.
Depuis plus de 50 ans, le procédé FLOAT est la méthode la plus couramment utilisée dans le monde. Elle permet d’obtenir de nombreuses gammes de verres en fonction de leur épaisseur. La qualité du verre se réfère à des caractéristiques dimensionnelles et physiques. En France et en Europe, la norme qui détaille l’ensemble de ces caractéristiques est la NF-EN 572-2.
Verre plat : les différentes utilisations
La demande et la production de verre plat n’a pas cessé d’augmenter ces dernières années. En 2016, elle représentait 72 millions de tonnes contre 33 millions de tonnes en 2010. Très présent dans les marchés du bâtiment et de l’automobile, le verre plat voit ses emplois variés en fonction du processus de création.
On retrouve en majorité les utilisations suivantes :
- Les vitrages traditionnels transparents
- Les vitrages de sécurité et de grande résistance : armé, feuilleté et trempé
- Les vitrages “intelligents” : anti-reflets, réfléchissants, autonettoyants…
- Les miroirs de toutes tailles
Parmi les nombreux vitrages réalisés avec du verre plat on retrouve différentes applications allant de la paroi vitrée à l’isolation thermique ou acoustique, mais également à la protection incendie ou le contrôle solaire.
Le verre plat représente aujourd’hui un réel défi écologique pour le gouvernement français. L’engagement pris par l’état pour la croissance verte représente un objectif de 40 000 tonnes, soit un recyclage de 20 % des déchets issus de la mise en décharge de fenêtres. Un but qui impactera également toutes les entreprises du secteur dans les années à venir.